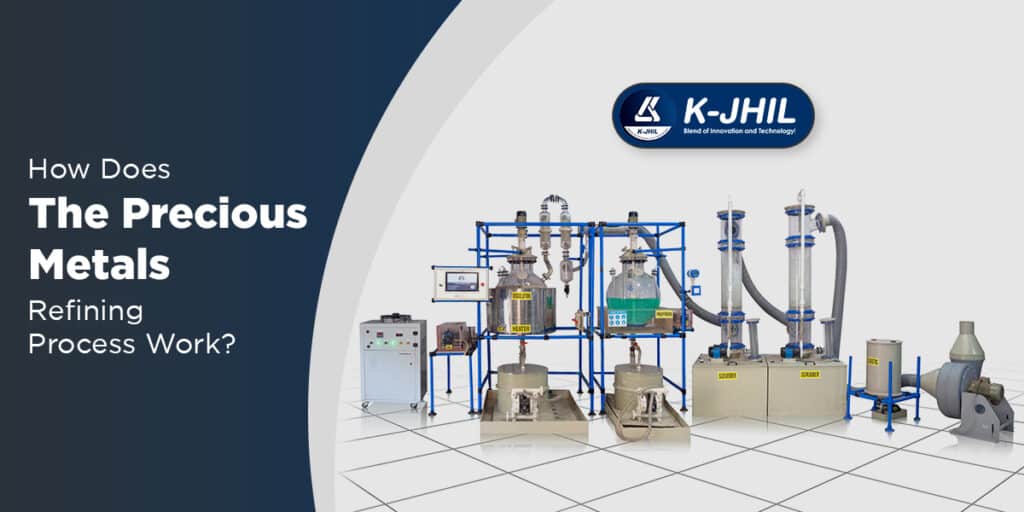
Purifying precious metals in their purest form has proven to be a difficult endeavor. Although rare earth elements have increasingly become difficult to source, they are used to produce various finished products.
Since we are professionals working in this area, we are aware of the complexity of the refining process. We are fully aware that attaining purity is not only a technical problem but also an environmental and economic issue.
The effectiveness of the precious metals refinery process is the key to overcoming the kind of hindrances described above. The goal of this blog is to shed light on how the final products are made out of raw, valuable materials.
What's on this page:
What is the Refining Process of Gold?
Understanding the precious metals refining process offers insights into gold’s transformation. Here are the steps in the refining process of gold.
Initial Processing and Crushing
The journey of gold from ore to a refined product begins here. First, the raw gold-bearing material is collected. This stage is crucial for setting the foundation for purity.
Next, the ore undergoes initial processing to separate gold from the surrounding rock. Crushing the ore is a vital step, breaking it down into small, manageable pieces. This process facilitates easier extraction of gold in subsequent stages.
Each step is meticulously planned to ensure maximum recovery of gold. Through crushing and initial processing, the stage is set for further refinement. This initial phase is foundational in the precious metals refining process.
Concentration and Removal of Impurities
After initial processing, concentration steps elevate the gold’s purity. Flotation, a key technique, utilizes chemicals like sodium cyanide to isolate gold. This stage is critical for removing bulk impurities.
During flotation, the mixture creates froth, allowing gold to separate from less dense materials. The precious metals refinery employs this method for its efficiency in concentrating gold. Subsequent leaching with cyanide solutions further dissolves residual impurities, refining the gold’s quality.
Post-concentration, gold is subjected to purification processes such as smelting, ensuring only the highest purity gold advances. These meticulous steps, from flotation to leaching, are essential for achieving the desired quality in the precious metals refining process.
Smelting and Producing the Pure Metal
Following concentration, smelting heats the gold to remove the remaining impurities. This high-temperature process separates the pure gold from other elements. Furnaces reach temperatures over 1,000°C, melting the concentrate into liquid gold.
In smelting, fluxes like borax and soda ash are added. These chemicals assist in separating gold from impurities, forming a slag on top. The pure, molten gold settles at the bottom, ready for further refining.
The final step involves cooling and solidifying the gold into bars or coins. This process, from smelting to casting, transforms concentrated gold into market-ready forms. Precision in temperature control and chemical use is crucial for achieving the highest purity of gold.
What is the Silver Refining Process?
Silver, like gold, undergoes a meticulous refining process to reach its purest state. This journey from ore to refined silver is complex. Here are the steps in the silver refining process.
Initial Sorting and Pre-treatment
The refining of silver begins with meticulous sorting and pre-treatment of ores. This initial step separates silver-rich materials from less valuable ones. Accurate sorting is crucial for efficiency and cost-effectiveness in the refining process.
Next, the pre-treatment involves crushing and grinding the ore. This prepares it for the chemical processes that extract silver. Roasting may follow, where ores are heated in air to convert sulfides into oxides, facilitating easier silver extraction.
Chemical leaching then plays a pivotal role. Solutions, often containing sodium cyanide, dissolve the silver from the ore. This method is selective, ensuring minimal silver loss and maximum purity in later stages.
Chemical Leaching and Separation
After pre-treatment, the silver enters the critical phase of chemical leaching and separation. This process extracts silver by dissolving it from the ore. A common agent in this phase is sodium cyanide, which selectively leeches silver.
The leached silver then undergoes a separation process to remove impurities. Merrill-Crowe or the Carbon in Pulp (CIP) method is often used. These techniques recover silver from the solution efficiently, ensuring purity.
At this stage, the precious metals refinery plays a crucial role. It employs advanced technology to refine the silver further, enhancing its quality. Equipment like leaching tanks and filters becomes vital, ensuring a smooth transition from ore to pure silver. This meticulous approach guarantees high-purity silver, ready for various applications.
Electrolytic Refining for Purity
Electrolytic refining elevates silver’s purity to remarkable levels. This process uses an electrolytic cell for purification. Silver acts as the anode in a solution of silver nitrate.
The electrical current causes silver to dissolve from the anode and deposit on the cathode. This method selectively purifies silver, removing base metals. The result is silver of 99.9% purity, ideal for industrial and jewelry use.
Equipment such as electrolytic cells and rectifiers are crucial for this phase. They ensure the precise control of current and purity levels. Through electrolytic refining, silver achieves the high standards required for global markets.
What are the Refining Processes for Other Precious Metals?
Beyond gold and silver, other precious metals undergo unique refining processes. Each metal requires specific methods tailored to its properties. Here are the steps involved in these refining processes.
Rare Earth Metals: Challenges and Methods
Refining rare earth metals presents unique challenges for precious metal refining companies. This is due to their similar chemical properties. These metals are crucial for high-tech applications, making their refinement critical. Their extraction and purification require precise and controlled processes.
Solvent extraction is a common method in refining rare earths. It separates metals using chemical solvents like hydrochloric acid. This process is effective but demands careful management to ensure environmental safety.
Ion exchange techniques are also employed, utilizing resins to capture specific metals from a solution. This method enhances the purity of rare earth metals, preparing them for use in various technologies. The refinement of rare earth metals, thus, combines complexity with the necessity for innovation and environmental consideration.
Final Thoughts
Precious metals refining is a complex process that requires a lot of knowledge, expertise, and resources.
We are one of the top precious metal systems providers. We prove our mettle in the field of precious metals refining thanks to our impressive set of features guaranteeing the best quality and efficiency. With systems capable of handling capacities up to 50kg to 100 tonnes, we serve both start-up or owner-operated small-scale artisans to large-scale industrial operators.
We have implemented high-performance equipment to allow us to reach 99.95% purity even in gold, silver, and platinum group metals refining. Such a result is a feat since it sets an industry benchmark. K-jhil Scientific’s product range includes Automatic Gold Refining and Semi-automatic Systems as well as Modular Systems, depending on the client’s needs. Our technology ensures low acid consumption, reducing environmental impact and operational costs.
Specializing in waste recovery, our systems effectively process low-grade gold wastes, including floor sweeps and polishing wash slurry, reclaiming valuable metals. Partner with us for cutting-edge refining solutions that promise accuracy, reliability, and unparalleled efficiency.